マイクロ流路チップ(デバイス)の製造方法は、使用する素材、製造するチップの複雑さ、精度要求、及びコストによって異なります。一般的な製造方法をいくつか紹介します。
ソフトリソグラフィー
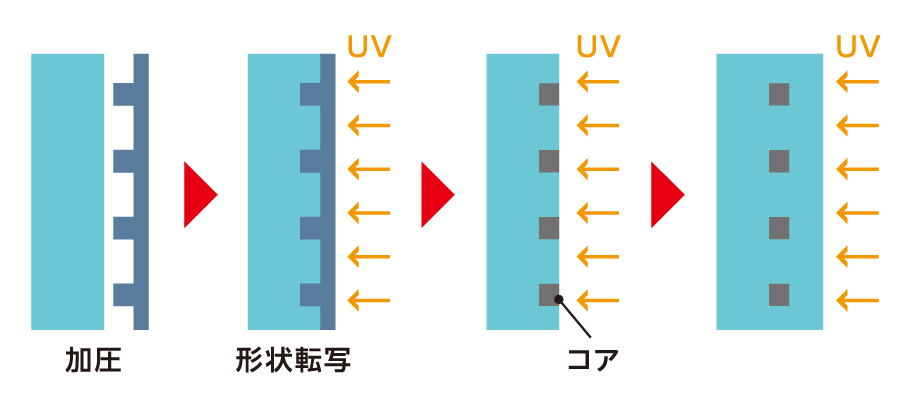
材料 | PDMS |
コスト | 比較的低コスト |
複雑形状、精度 | 中〜高精度。複雑な3D構造には限定されるが、微細な2Dパターンに適している。 |
よく使われる業界 | 半導体、ディスプレイ、バイオメディカル |
PDMS (ポリジメチルシロキサン) などを使用して、微細なパターンや構造を転写成形するための手法です。このプロセスでは、マスターモールド上にPDMSを流し込み、紫外線や熱で硬化させ脱型して作製した反転レプリカモールドを用いてマスターと同じ形状をUVレジストに形成します。柔らかいモールドで、Siウエハ等の転写対象に損傷を与えません。
フォトリソグラフィー
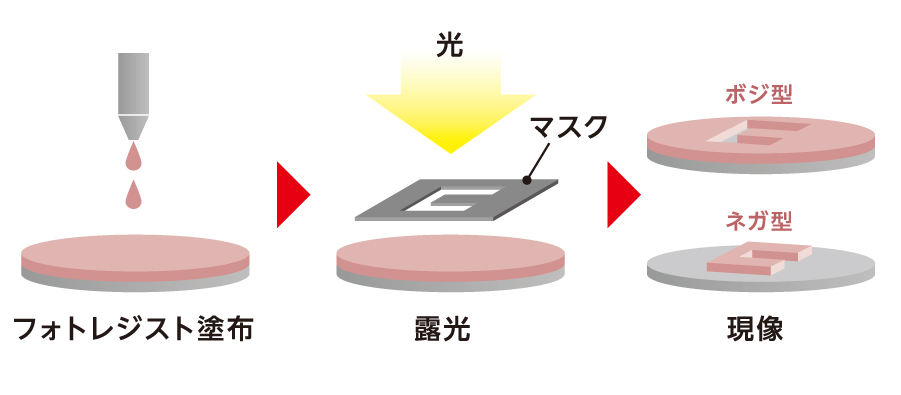
材料 | シリコン、ガラス |
コスト | 高コスト(クリーンルームが必要) |
複雑形状、精度 | 高精度。サブミクロンレベルの特性が可能。 |
よく使われる業界 | 半導体、センサー、MEMS、マイクロ流路 |
光によって感光性レジストを選択的に硬化させる手法で、微細加工に広く使用されます。マイクロ流路チップの製造では、サブミクロンの精度でマスターを作成するために使用されます。
インジェクション成形
.jpg)
材料 | 熱可塑性樹脂 |
コスト | 大量生産時は低コストだが、金型作成が初期コストとしてかかる。 |
複雑形状、精度 | 中精度。複雑な3D構造にも対応。 |
よく使われる業界 | 一般消費財、医療機器、自動車 |
プラスチック製のマイクロ流路チップを大量生産する場合に用いられます。溶融したプラスチックを型に注入して冷却し、固まった後に取り出します。熱硬化性樹脂であるPDMSでも大量生産時にインジェクション成形装置を使用しますが、熱可塑性樹脂用のインジェクション成形装置とは構造が異なります。
トランスファー成形
.jpg)
材料 | 高粘度PDMS、熱硬化性樹脂 |
コスト | 中コスト |
複雑形状、精度 | 中〜高精度。複雑な3D構造も可能。 |
よく使われる業界 | バイオメディカル、光学部品 |
高粘度PDMSを高い精度で気泡なく成形するのに適した成形手法です。材料は加圧されて型に押し込まれ、型の熱により硬化させます。
レーザーアブレーション
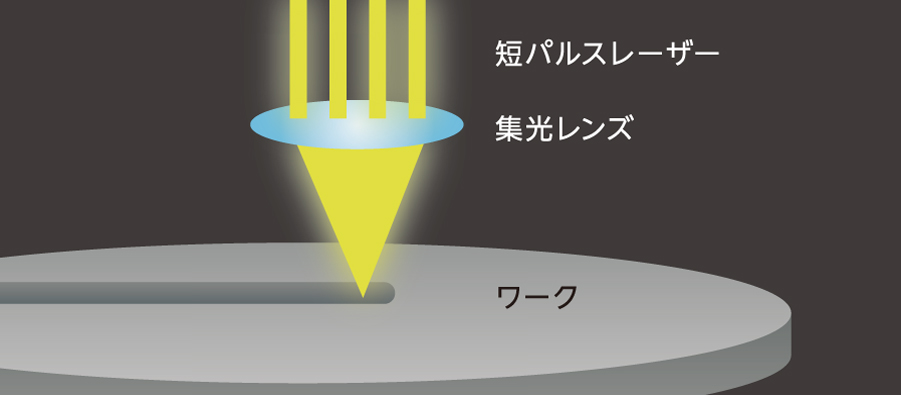
材料 | ガラス、ポリマー、金属 |
コスト | 高コスト |
複雑形状、精度 | 高精度。微細な特性が可能だが、3D構造は限定される。 |
よく使われる業界 | 高精度センサー、光学部品 |
高エネルギーのレーザーを使用して材料を分解除去し、微細な構造や流路を作製する方法です。硬度が高く、割れ易い材料への精密加工に適しますが、加熱による材質の変化や分解飛散した微細粒子の再付着等の課題が残ります。
3Dプリント
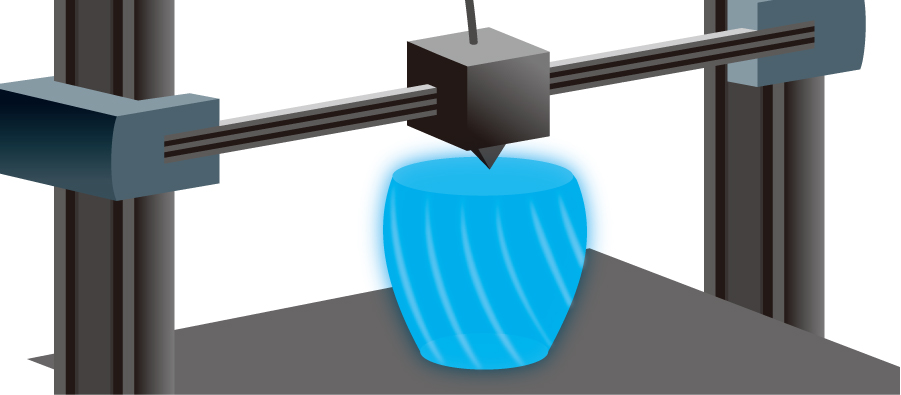
材料 | 樹脂(3Dプリンタ依存) |
コスト | 中〜高コスト。生産規模に依存。 |
複雑形状、精度 | 中精度。非常に複雑な3D構造が可能だが、3Dプリンタの性能に左右される。 |
よく使われる業界 | プロトタイピング、医療機器、航空宇宙 |
近年、3Dプリンティング技術が進化しており、微細な3D構造を直接プリントすることでマイクロ流路チップを作成することができます。